Quality
A descriptive paragraph that tells clients how good you are and proves that you are the best choice that they’ve made.
Quality & Traceability
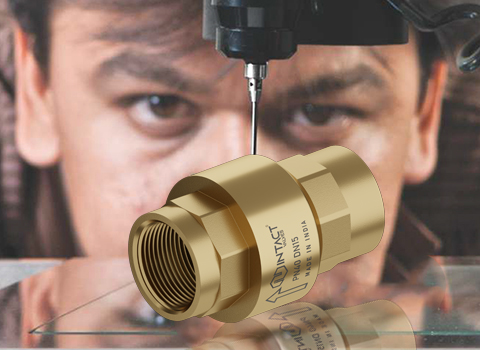
We aim to provide quality products and achieve the established objectives of continuous improvement with a full undertaking of all legal and regulatory requirements.
Our Quality systems and procedures are observed by all employees and are promoted and enforced by senior management with awareness meetings and training with the specific aim of continually improving the professionalism of all our people.
A company also accredited by ISO 9001:2015 and operates within the guidelines of such.
Quality is one of the Core Value of the Company
RAW MATERIAL INSPECTION
Raw material quality is vital for valve quality, Intact Valve source casting, and forging from the selected vendors.
Before machining, we always take 4 steps to guarantee the raw material quality:
- Visual Test: Visual test as per norms
- Valve wall thickness test: Random inspection of valve wall thickness by ultrasonic thickness meter
- Chemical Component analysis: Random PMI test is performed to ensure qualification.
- Dimension Check face to face; flange thickness will be checked before the process.
PRODUCTION
When the designs are approved by the customer, the production process starts. Our highly qualified staff works with high-speed machines to produce valves accordingly as per requirement. After rough machining, 20% of valve component is checked dimensionally by Q.C inspectors and 100% after fine machining.
VALVE TESTING
After the production process is finished 100% of valves are tested in-house. Our valves have to ensure a hydro-test on the body and seat, followed by a low pressure air-test in excess of requirements, prior to shipping. Additional tests on valves and materials can also be arranged by Intact Valves.
The following standard performance test are performed according to norms, or to customer specific requirements:
- Visual & Dimensional Check
- Hydrostatic Testing
- Low Pressure Gas Seat Testing
- High Pressure Gas Testing
- Cryogenic Gas Testing Down To -196 “ (-320,8 a F)
- High Temperature Testing Up To 660″ (1220 a F)
- Fugitive Emission Gas Testing
- Antistatic Testing
- Torque Testing
- Cavity Relief Testing
- Double Block & Bleed (DBB) Testing
- Double Isolation & Bleed (DIB-1, DIB-2) Testing
PACKING & SHIPPING
We follow the safe and Intact standard export packing considering the longer transit by sea shipments that can damage the valves and specifically painting of the valves. If the packing is not performed with extra safety the final goods reached to the customer may not be in position as it’s shipped.
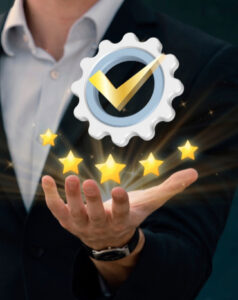
Quality Control & Testing Facility
We have testing facilities for hydraulic testing & pneumatic testing. All the valves are strictly tested as per the international standards. The industrial valves manufactured by us, portable hydro – pneumatics pumps test hydraulic pressure of any fitting or valves up to 5000 PSI. Media of Fluid : Pure Water, Air Compressors : to test any fitting of valves pneumatically up to 150 PSI or as per the requirement.
Our company follows strict quality standards that are in accordance with international quality standards. We follow stringent quality control, testing and inspection at every level of the factory inputs and closely monitor the different assembly levels and manufacturing procedures. This assures trouble free performance of the valves.
Good Quality = Good Services = Good Prices Its Intact Valve
- Wide range of valves.
- Dedicated work force.
- Offer market-leading prices.
- Wide network areas.
- International quality standards.
- Use of advanced technology.
- Use of qualitative raw material.
- Prompt Delivery.
- Safe packaging.
- Customization facilities.
- Ethical business policies.
- R & D.